Basics of Structural Analysis: Difference between revisions
(77 intermediate revisions by the same user not shown) | |||
Line 3: | Line 3: | ||
Structural analysis using about high school level physics and maths. | Structural analysis using about high school level physics and maths. | ||
The terms used | |||
* <math>E</math> Young's modulus <math>\sigma = E\epsilon</math> is to be compared to <math>F= kx</math> | |||
* <math>\sigma</math> is the stress (force) in the material. It is defined as <math>\sigma = \frac{F}{A}</math> | |||
* <math>\sigma_{cr}</math> Critical stress. | |||
* <math>\sigma_{cr}</math> | |||
* <math>\sigma_{cr}</math> | |||
* <math>\sigma_{cr}</math> | |||
* <math>\epsilon</math> is the strain or deformation (displacement) in the object (perhaps in the dimension of length ratio): <math>\epsilon = \frac{\partial}{\partial X}(x-X)= F'-I</math> where <math>X</math> is the reference position of material. For a uniform bar <math>\epsilon = \frac{\Delta L}{L} = \frac{\sigma}{E} = \frac{F}{AE}</math>. | |||
* <math>\lambda</math> is the stretch ratio: <math>\lambda = \frac{L+\Delta L}{L}</math> | |||
* <math>\nu</math> Poisson ratio is a measure of deformation of material. <math>\nu = - \frac{d \epsilon_y}{d \epsilon_x}</math> | |||
* <math></math> | |||
== Basic theory == | == Basic theory == | ||
Line 13: | Line 24: | ||
Virtual work principle. | Virtual work principle. | ||
Dead loads, live loads, impact loads (impact factor), wind loads. | |||
Equilibrium. | |||
Forces: | |||
* Normal force and axial force (out-of-plane forces, in-plane forces) | |||
* Shearing force <math>\frac{V(x)}{x} = -w(x) </math>. Thus we have <math>\Delta V =\int w(x) dx </math>. <math>w(x)</math> is the intensity of applied (normal?) force. | |||
* Bending moment <math>\frac{dM}{dx} = V(x)</Math> and thus <math>\frac{d^2M}{dx^2} = -w(x)</Math>. | |||
* Torsion (of a plate) | |||
* Curvature and twist | |||
Hooke's law hold for linear elastic material: <math>\epsilon = \frac{\sigma}{E}</math>, where <math>\sigma</math> is the bending stress. The force <math>\delta P</math> is <math>\delta P = \sigma \delta A</math>. '''Yield point''' (strength) is when Hooke's law is not acceptable anymore; the limit of elastic behavior. It is often used to determine the maximum allowable load in the component. | |||
Buckling is a process by which a structure cannot withstand loads so it must change its shape. | |||
Stable equilibrium is when the force (pressure) applied doesn't reach the critical load, allowing the structure to return to its original equilibrium. | |||
== Plate == | == Plate == | ||
* Torsion (of a plate) | |||
* Curvature and twist <math>T_{xy}</math>. | |||
Curvature in the <math>x</math> direction <math>\kappa_x = \frac1{R_x}</math> is the rate of change of the slope with respect to arch length, giving | |||
<math> | |||
\kappa_x = \frac{\frac{\partial^2 w}{\partial x^2}} | |||
{\sqrt{(1 + \left(\frac{\partial w}{\partial x} \right)^2}^3} | |||
</math> | |||
Strains in a plate <math>\epsilon_{xx}</math>. | |||
Von Kármán strains. | |||
== Beam == | == Beam == | ||
Forces: | |||
* Normal force and axial force | |||
* Shearing force <math>\frac{V(x)}{x} = -w(x) </math>. Thus we have <math>\Delta V =\int w(x) dx </math>. <math>w(x)</math> is the intensity of applied (normal?) force. | |||
* Bending moment <math>\frac{dM}{dx} = V(x)</Math> and thus <math>\frac{d^2M}{dx^2} = -w(x)</Math>. | |||
=== Deflection of beams === | |||
[[File:BeamDeflection.svg|thumb|The deflection of a beam.]] | |||
The strain <math>\epsilon</math> in the filament is due to the different lengths of filaments in bended beam. <math>\epsilon = \frac{\ell_1 - \ell}{\ell} = \frac{\Delta y}{R}</math> which for linear elastic material (using Hooke's law) gives | |||
<math> \frac\sigma E = \frac{\Delta y}{R} = \epsilon</math> where <math>\sigma</math> is bending stress | |||
Radius of curvature <math>\frac1R = \frac{\partial v^2}{\partial x^2}</math>, and <math>\epsilon_{xx} = -y \frac{\partial^2 v}{\partial x^2}</math>. | |||
== Column == | == Column == | ||
Line 22: | Line 81: | ||
Column is a vertical beam. | Column is a vertical beam. | ||
== Pipe == | == Cylindrical Pipe == | ||
[[File:AxialStress.svg|thumb|Axial stress]] | |||
Cylinder stress | |||
* Axial (Longitudinal) stress <math>\sigma_a</math> | |||
* Tangential (hoop or circumferential) stress <math>\sigma_t</math> | |||
* Radial stress <math>\sigma_r</math> | |||
=== | === Axial stress === | ||
The axial stress is uniform across the cylinder wall. The stress is found by equilibrium calculations (see below). See the difference between external and internal pressure. | |||
'''External pressure''' | |||
The critical stress is <math>\sigma_{cr} = \frac{F}t = \frac{RE}{S(1-\nu^2)}</math>, where <math>E</math> is the Young's modulus, <math>\nu</math> is the Poisson ratio, <math>R</math> is the radius of the shell and . . .[Not ok. . . , see https://core.ac.uk/download/pdf/10851171.pdf page 28. ] | |||
'''Internal pressure''' | |||
The force <math>p_iA_i</math> from the internal pressure is equilibrated by the wall stress <math>\sigma_a A_a = \sigma_a (A_o - A_i)</math> where <math>A_i</math> is internal area and <math>A_o</math> is the outer area. | |||
The force on the direction of axis (from center to the loop) due to the internal pressure is | |||
<math> | |||
F = \int_0^r 2 p \pi r dr = 2 p \pi \frac{r^2}{2} = p \pi \frac{D^2}{4} | |||
</math> | |||
The axial stress is <math>\sigma_L = \frac{F}{A} = \frac{p\pi \frac{D^2}{4} }{\pi D t} = \frac{pD}{4t}</math> | |||
=== The pressure effect === | |||
The longitudinal stress and hoop (radial) stress. | |||
<math>\sigma_L = \frac{pD}{4t}</math> where <math>p</math> is the internal pressure, <math>D</math> is the mean diameter of cylinder and <math>t</math> is the wall thickness. Also, <math>\sigma_H = \frac{pD}{2t}</math>. | |||
Applying Hooke's law and the fact that <math>\sigma_H = 2\sigma_L</math> we get | |||
<math> | |||
\sigma_L = \frac{\epsilon_L + v\epsilon_H}{1-\nu^2}E = \frac{\epsilon_H}{2-\nu}E | |||
</math> | |||
where <math>\nu</math> is the Poisson's ratio and <math>E</math> is the Young's modulus. | |||
=== Buckling of cylinders === | |||
The differential equation of the classical buckling theory of a thin-walled shell. . . | |||
Analytic solution. | |||
=== Fiberglass (Glassfiber) Cansat === | |||
Also impact strength should be considered as the explosion is hard. | |||
The stress is in general defined by <math>\sigma = \frac FA</math>. However, the area changes (usually grows: spreads laterally) while compressing. While in Hooke's regime, we have <math>\sigma = E\epsilon</math>, where <math>E</math> is Young's modulus and <math>\epsilon</math> is the strain (deformation) <math>\epsilon = \frac{\Delta \ell}{\ell}</math>. In this region the material deforms elastically and returns to its original shape. | |||
The longitudinal stress of cylindrical pipe is <math>\sigma_L = \frac{F}{4t}</math>, where <math>F</math> is the applied force, <math>E</math> is the Young's modulus. | |||
The diameter of the cansat can is <math>D=66</math> mm. Thickness <math>t</math> is to be determined. The force <math>F</math> acting on the soda can when the payload is ejected from the rocket is CHECK this <math>F=700</math> N. | |||
Thus, we will have for the thickness <math>t = \frac{F}{4\sigma_L} = frac{700 N}{4}</math>. | |||
Compressive stress is the capacity of a material to withstand loads tending to reduce size. | |||
Fibreglass is fibre-reinforced plastic, in which the fibres originates from glass, carbon, aramid or basalt, usually. The polymer is usually an [https://en.wikipedia.org/wiki/Epoxy epoxy], [https://en.wikipedia.org/wiki/Vinyl_ester vinyl ester] or [https://en.wikipedia.org/wiki/Resin resin] (hartsi in Finnish, vaik in Estonian). The polyester resin is liquid, which will solidify when the hardener is added. The hardener ([https://en.wikipedia.org/wiki/Methyl_ethyl_ketone_peroxide Methyl Ethyl Ketone Peroxide]). | |||
However, below is structural properties of glass fiber. Normal glass fiber is E-glass, which is alumino-borosilicate glass with less than 1% alkali oxides. See more details at https://kevra.fi/?s=lasikuitu or https://composite24.ee/tooted/kangas-ja-kiud | |||
{| class="wikitable" | |||
|+ The Young's modulus | |||
|- | |||
! !! Tensile strength [MPa] !! Compressive strength [MPa] !! Yield strength [Mpa] !! Ultimate strength [Mpa] !! Young's modulus E [GPa] !! Density g/cm<sup>3</sup> | |||
|- | |||
| E glass || 3445 || 1080 || - || 5650 || 76 || 2.58 | |||
|- | |||
| Unsaturated polyester || 90 || 55 || 3.23 || || || 1.35 | |||
|- | |||
| Epoxy || || - || 26-85 || || 3 || 1.35 | |||
|- | |||
| S-2 || 4890 || 1600 || 85.5 | |||
|} | |||
The fiber is usually made to be a ''fabric'' or ''mat'' (or more). | |||
* Thickness of the fabric is between 0.04 mm and 0.23, usually. | |||
* | |||
== References == | == References == | ||
https://scholarshare.temple.edu/bitstream/handle/20.500.12613/7150/Udoeyo-Textbook-2020.pdf?sequence=1 | |||
https://tiij.org/issues/issues/spring2006/12_Dues-Accepted/Dues.pdf | |||
https://core.ac.uk/download/pdf/10851171.pdf | |||
https://www.sciencedirect.com/science/article/abs/pii/S0263823101000660 Paywall | |||
[https://gigvvy.com/journals/ijase/articles/ijase-201702-14-3-121.pdf Mechanical Properties of Glass Fiber Reinforced Polyester Composites] | |||
https://www.engineeringtoolbox.com/young-modulus-d_417.html#gsc.tab=0 The table for strengths. | |||
http://k-mac-plastics.com/data-sheets/fiberglass_technical_data.htm |
Latest revision as of 10:19, 23 January 2024
Introduction
Structural analysis using about high school level physics and maths.
The terms used
- Young's modulus is to be compared to
- is the stress (force) in the material. It is defined as
- Critical stress.
- is the strain or deformation (displacement) in the object (perhaps in the dimension of length ratio): where is the reference position of material. For a uniform bar .
- is the stretch ratio:
- Poisson ratio is a measure of deformation of material.
Basic theory
Principle of superposition: linearity. Displacement at location from forces and </math>P_2</math> located at different positions is calculated as
The energy principle: giving the total energy as which is called strain energy. For linear deformation this gives .
Virtual work principle.
Dead loads, live loads, impact loads (impact factor), wind loads.
Equilibrium.
Forces:
- Normal force and axial force (out-of-plane forces, in-plane forces)
- Shearing force . Thus we have . is the intensity of applied (normal?) force.
- Bending moment and thus .
- Torsion (of a plate)
- Curvature and twist
Hooke's law hold for linear elastic material: , where is the bending stress. The force is . Yield point (strength) is when Hooke's law is not acceptable anymore; the limit of elastic behavior. It is often used to determine the maximum allowable load in the component.
Buckling is a process by which a structure cannot withstand loads so it must change its shape. Stable equilibrium is when the force (pressure) applied doesn't reach the critical load, allowing the structure to return to its original equilibrium.
Plate
- Torsion (of a plate)
- Curvature and twist Failed to parse (SVG (MathML can be enabled via browser plugin): Invalid response ("Math extension cannot connect to Restbase.") from server "https://wikimedia.org/api/rest_v1/":): {\displaystyle T_{xy}} .
Curvature in the direction is the rate of change of the slope with respect to arch length, giving
Strains in a plate .
Von Kármán strains.
Beam
Forces:
- Normal force and axial force
- Shearing force . Thus we have . is the intensity of applied (normal?) force.
- Bending moment and thus .
Deflection of beams
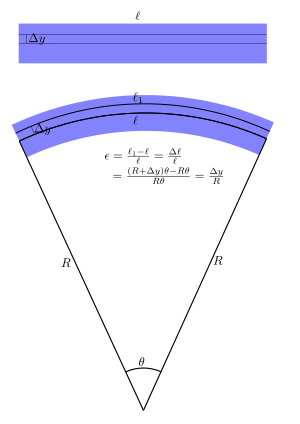
The strain in the filament is due to the different lengths of filaments in bended beam. which for linear elastic material (using Hooke's law) gives where is bending stress
Radius of curvature , and .
Column
Column is a vertical beam.
Cylindrical Pipe
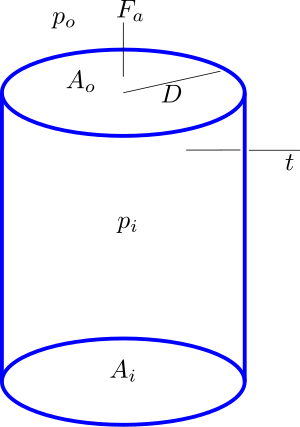
Cylinder stress
- Axial (Longitudinal) stress
- Tangential (hoop or circumferential) stress
- Radial stress
Axial stress
The axial stress is uniform across the cylinder wall. The stress is found by equilibrium calculations (see below). See the difference between external and internal pressure.
External pressure
The critical stress is , where is the Young's modulus, is the Poisson ratio, is the radius of the shell and . . .[Not ok. . . , see https://core.ac.uk/download/pdf/10851171.pdf page 28. ]
Internal pressure
The force from the internal pressure is equilibrated by the wall stress where is internal area and is the outer area.
The force on the direction of axis (from center to the loop) due to the internal pressure is
The axial stress is
The pressure effect
The longitudinal stress and hoop (radial) stress.
where is the internal pressure, is the mean diameter of cylinder and is the wall thickness. Also, .
Applying Hooke's law and the fact that we get
where is the Poisson's ratio and is the Young's modulus.
Buckling of cylinders
The differential equation of the classical buckling theory of a thin-walled shell. . .
Analytic solution.
Fiberglass (Glassfiber) Cansat
Also impact strength should be considered as the explosion is hard.
The stress is in general defined by . However, the area changes (usually grows: spreads laterally) while compressing. While in Hooke's regime, we have , where is Young's modulus and is the strain (deformation) . In this region the material deforms elastically and returns to its original shape.
The longitudinal stress of cylindrical pipe is , where is the applied force, is the Young's modulus.
The diameter of the cansat can is mm. Thickness is to be determined. The force acting on the soda can when the payload is ejected from the rocket is CHECK this N.
Thus, we will have for the thickness .
Compressive stress is the capacity of a material to withstand loads tending to reduce size.
Fibreglass is fibre-reinforced plastic, in which the fibres originates from glass, carbon, aramid or basalt, usually. The polymer is usually an epoxy, vinyl ester or resin (hartsi in Finnish, vaik in Estonian). The polyester resin is liquid, which will solidify when the hardener is added. The hardener (Methyl Ethyl Ketone Peroxide).
However, below is structural properties of glass fiber. Normal glass fiber is E-glass, which is alumino-borosilicate glass with less than 1% alkali oxides. See more details at https://kevra.fi/?s=lasikuitu or https://composite24.ee/tooted/kangas-ja-kiud
Tensile strength [MPa] | Compressive strength [MPa] | Yield strength [Mpa] | Ultimate strength [Mpa] | Young's modulus E [GPa] | Density g/cm3 | |
---|---|---|---|---|---|---|
E glass | 3445 | 1080 | - | 5650 | 76 | 2.58 |
Unsaturated polyester | 90 | 55 | 3.23 | 1.35 | ||
Epoxy | - | 26-85 | 3 | 1.35 | ||
S-2 | 4890 | 1600 | 85.5 |
The fiber is usually made to be a fabric or mat (or more).
- Thickness of the fabric is between 0.04 mm and 0.23, usually.
References
https://tiij.org/issues/issues/spring2006/12_Dues-Accepted/Dues.pdf
https://core.ac.uk/download/pdf/10851171.pdf
https://www.sciencedirect.com/science/article/abs/pii/S0263823101000660 Paywall
Mechanical Properties of Glass Fiber Reinforced Polyester Composites
https://www.engineeringtoolbox.com/young-modulus-d_417.html#gsc.tab=0 The table for strengths.
http://k-mac-plastics.com/data-sheets/fiberglass_technical_data.htm